Crystalline Thermoplastics: A Quick Study
We are looking at crystalline materials, among crystalline resins, common materials considered for working components in industrial applications include, Acetals, Nylons, PBTs, and a new one POK. Non-common materials, considered specialty resins are PPS, PEEK, and PI. There are others, and even cost-effective talc filled PP gets used from time to time when demands are not onerous.
Amorphous materials such as ABS, HIPS (High Impact Polystyrene), Noryl, Polycarbonate, Polyether Sulfone, Polysulfone, and PEI(Ultem).
How do these differ?
Typically, amorphous materials are clear (but not always), they have lower shrinkage values, so they warp less during molding, have high friction/poor wear, poor chemical resistance, and a different temperature curve of property (such as flexural strength) versus heat. Amorphous materials have flex strength curves that are more linear, and lower at lower temperatures, but maintain properties until a softening point.
Crystalline materials have higher values at the lower temperatures, then a dramatic drop at the glass transition temperatures. Glass fiber filling of crystalline materials dramatically improve this performance. Amorphous materials are more often used for enclosures or parts requiring good aesthetics.
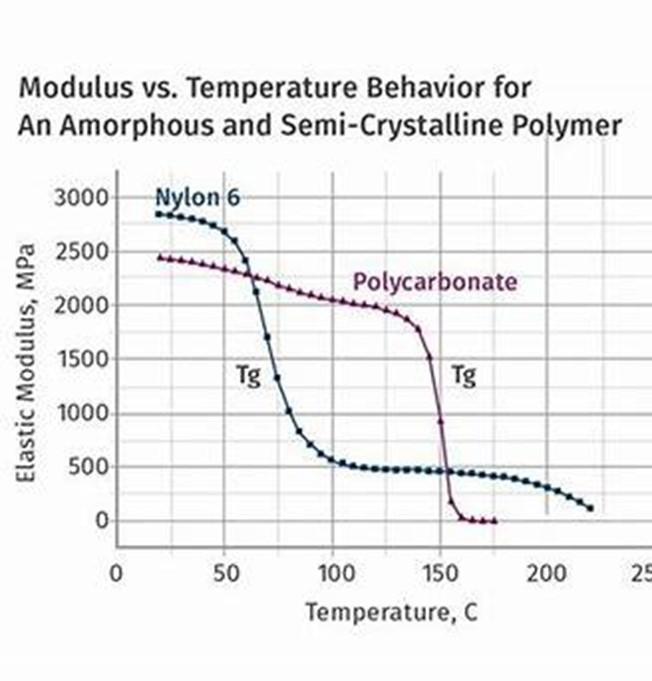
What makes an engineer consider one over the other?
Depends on the engineer. It should be the least expensive option that gets the job done without a lot of testing prior to production for low quantity type production applications. Experience with resin satisfies that issue, but for high volume application, assurance that the material with the lowest cost gets chosen will require life testing.
Sometimes corporate goals such as a green initiative can play a factor as well. There are answers here.
Acetals, trade named Delrin, Celcon, and Duracon for example occupy the low cost bracket. Decent friction, wear, high flexural modulus, low moisture absorption are strong points. Unless impact modifiers are used, impact strength is low. Addition of glass fibers reduces impact strength further, but stiffness is increased. This resin has very good fatigue resistance. A negative for molders is the smell of formaldehyde that is quite upsetting during purging or when the material is over heated. Applications shouldn’t exceed 150F in the long term. Specific gravity of 1.42 increases cost per cubic inch compared to nylon 6 and 6/6. There is high shrinkage, resulting in increased warpage, voids, and sinks with thicker wall sections. Surface finish is sometimes difficult to process away. They are easy to acquire as rod stock to prototype, difficult to 3D print due to shrinkage. Sometimes we see machined parts from Acetal transitioning to molded parts as volume grows. There is copolymer, and homopolymer versions with minor differences. Homopolymer have better stiffness, and higher heat resistance to a minor extent, while copolymers process more easily and have better impact. Again, additive packages for both types blur these lines. A Delrin 100T has far better impact than Celcon M90 for example.
Nylons are more commonly used and have far more variants. Nylon4, 6, 6/6, 6/7, 7 9, 10,11,12 are examples of this diverse universe, all with a place at the table when specific requirements dictate. We will see shortly how POK makes them somewhat redundant, however. Starting at Nylon 4 and going to Nylon 12 the amount of water absorption decreases, the temperature resistance reduces, vapor transmission reduces, clarity gets better, and dry as molded impact strength improves. When trying to define nylons there is a broad spectrum, especially when additives get included. Glass fiber is a big game changer, nylon really likes to bind to the sizing agents on the glass fiber so major gains in performance with small amounts (13%) of glass fiber are added, Add an impact grade of 6/6 Nylon along with the glass fiber and a very durable material with little moisture encumbrances results. What hurt glass filled nylon in electronic applications in the 1970’s was the poor performance when flammability additives were added. They were conductive. That’s when PBT resins took nylon’s place in that industry. Nylons are less slippery than Acetals, but again additives such as Carbon fiber, PTFE, UHMW, greases, and Kevlar fibers make them attractive friction/wear choices.
High temperature Nylons: PPA (Amodel), and 4/6 nylons have slightly higher(20-40F) temperature capabilities than standard grade with higher pricing.
Nylon has been at the forefront of metal replacement initiatives. From under hood in automotive, to aluminum die cast parts. There seems to be greater acceptance to the material’s capability for strength, performance in hot applications, and chemical environments. While GF 6/6 nylons can be used in radiator applications, one side of the part has to be exposed to atmosphere, a kind of strange drawback. A second weak point is nylon’s lack of resistance to alcohols in gasoline. Many carburetors have been clogged with decomposed Nylon components. For submerged cooling, the high temp. nylons are used. A 60% long glass fiber 6/6 nylon, with UV protection, heat stabilizers, and lubrication additive package is a formidable structural option. They can and will absorb a lot of moisture, up to 3% (6 and 6/6 versions) in some environments with attendant dimensional changes. When in sub-freezing, low dew point applications, without the impact packages nylons can have very low impact values. You will always see data with “dry as molded” and “conditioned” value that are quite different. Nylons also have serious shrinkage issues and warp when thick and thin wall are present on a single part. The thick sections can shrink at .030” inches per inch, and thin walls at .010”.
Polyesters, PBT and PET. We are going to talk about thermoplastic polyesters, not thermosets which all cross link during processing. One thinks of boats when polyester is discussed, but low profile, bulk molding compounds of polyester, glass fiber, various fillers, and a little polystyrene for surface appearance have need used in automotive, and high-capacity electrical devices for over 60 years.
Thermoplastic polyesters such as Valox, Rynite, and Celanex started to be used more broadly in the 1970’s when it was found that V-0 additives were more compatible than with nylons. Weld line strengths were not as diminished, and electrical properties were maintained with PBT in comparison to nylons.PBT is more apt to be used when fillers are not required, and PET which is not as process friendly gets used when filled with Glass or carbon fiber. PET is less crystalline as evidenced in clear soda bottles, and does not process as quickly as PBT without an additive package. An early application for PBT was in water pumps for outboard motors, and it performed well until temperatures exceeded 150F when it’s well known depolymerization when moisture is present took place. During processing PBTs can very easily be compromised when not dried adequately, and because it does not show up visually can be a significant problem. An impact test with finished parts is the fastest and best method of insuring adequate drying.
POK, known as Polyketone is the new comer, and it has great potential. It is made from 50% flue gas from electric generation facilities, so is considered “green”. Property wise, mechanically it falls between Acetals and 6/6nylons. It has better chemical resistance than both. It has very low water absorption like Acetals, but higher impact strength more typical of a toughened nylon. Friction is very low, better than Nylon and Acetal. It is more susceptible to warp with differential mold temperatures (it will preferentially warp towards the hot side of a mold to a controlled and greater degree than other materials. Cost is comparable to toughened nylons. A unique aspect is that while it has been around for over 20 years it never became competitive until it was acquired by a Korean company that spent an amazing amount of money fully trouble shooting manufacturing, documenting properties, and getting certifications across the globe before widespread implementation across the industry. US and Eu approvals for Dairy exposure for example were in place very early in the ramp up. A worldwide certificate for a V-0 flammability rating with good impact strength, elongation, and flexibility is a big advantage. A negative aspect (or positive from a user’s perspective) is that when left at processing temperatures for 15 minutes or more, it starts to crosslink and has poor flow. Processors need to keep on their toes. This means long term constantly improving heat tolerance.
How do these materials compare with each other in real world applications and real-world issues such as weld line strength? Nylon has better weld line strength, POK a close second, PBT next and finally Acetal. When glass fibers are introduced, these comparisons change to PBT first, POK next, then Nylon and Acetal. Chemical resistance has POK the clear winner with each of the others having specific weak points such as alcohol for Nylon, and water for PBT. Acetals have always been used for inexpensive wear items like rollers, or pulleys due to good friction, low wear, and high modulus. POK will be taking some of this marketplace with even lower friction, better wear and quieter operation.
Where does talc-filled polypropylene fit in this cast?
Unfilled PP is considered a commodity resin, used in packaging, fishing tackle boxes for example, and never really considered an engineering material. Talc filled/glass filled PP has demonstrated a capable presence in lower temperature structural applications with very attractive pricing, chemical resistance, and satisfactory impact strength. Automotive applications got everyone’s attention at the beginning, air cleaner housings for example, then dashboard structure (versus cosmetic) applications. When the quantities are high, the loads light, and cost is very important, filled PP needs to be considered. The breakthrough for this performance has been getting superior binding systems to lock fibers to the resin.
These crystalline materials have been the favorites when looking at metal replacement applications. Glass or carbon fiber concentrations of up to 60% in Nylons (including long glass fibers, and long fiber polypropylene) are the first cost effective candidates. High stiffness, working temperatures of 200F or higher long-term, built-in color, decent impact values all contribute to the popularity of these materials.